When fossil fuels are utilized in combustion processes to run boilers, furnaces, or other equipment, they can release SO2 or SO3 as part of the exhaust gas. These sulfur oxides react easily with other elements to form harmful compounds such as sulfuric acid and can negatively affect human health and the environment. Due to these potential effects, control of this compound in flue gases is an essential part of coal-fired power plants and other industrial applications.
Due to erosion, plugging, and build-up concerns, one of the most reliable systems to control these emissions is an open-tower wet flue gas desulfurization (FGD) process using a limestone, hydrated lime, seawater, or other alkaline solution. Spray nozzles can effectively and reliably distribute these slurries into absorption towers. By creating uniform patterns of properly sized droplets, these nozzles can effectively create the surface area needed for proper absorption while minimizing the entrainment of the scrubbing solution into the flue gas.
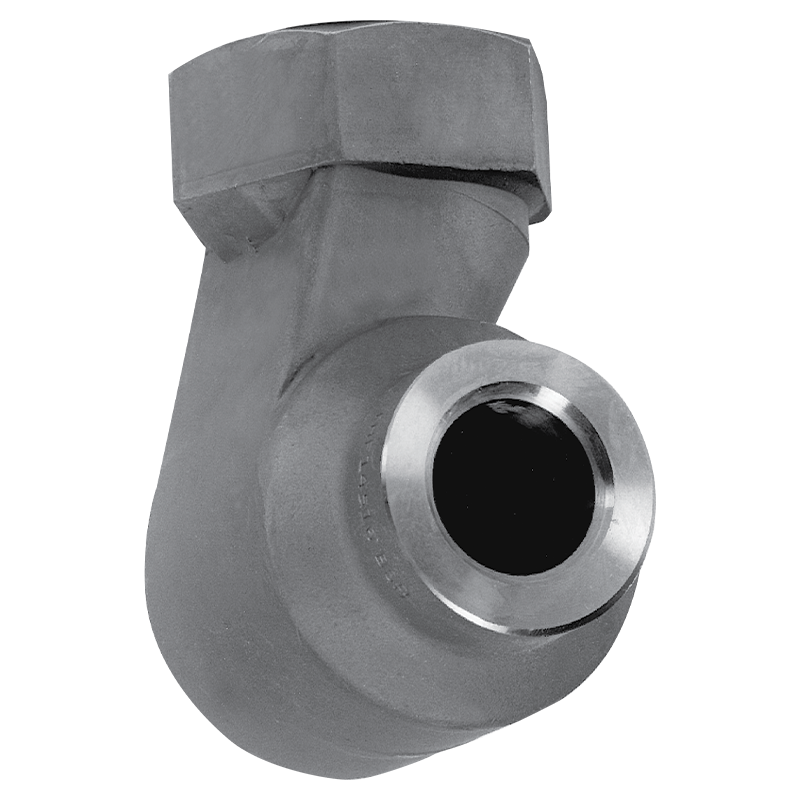
Common Uses And Industries
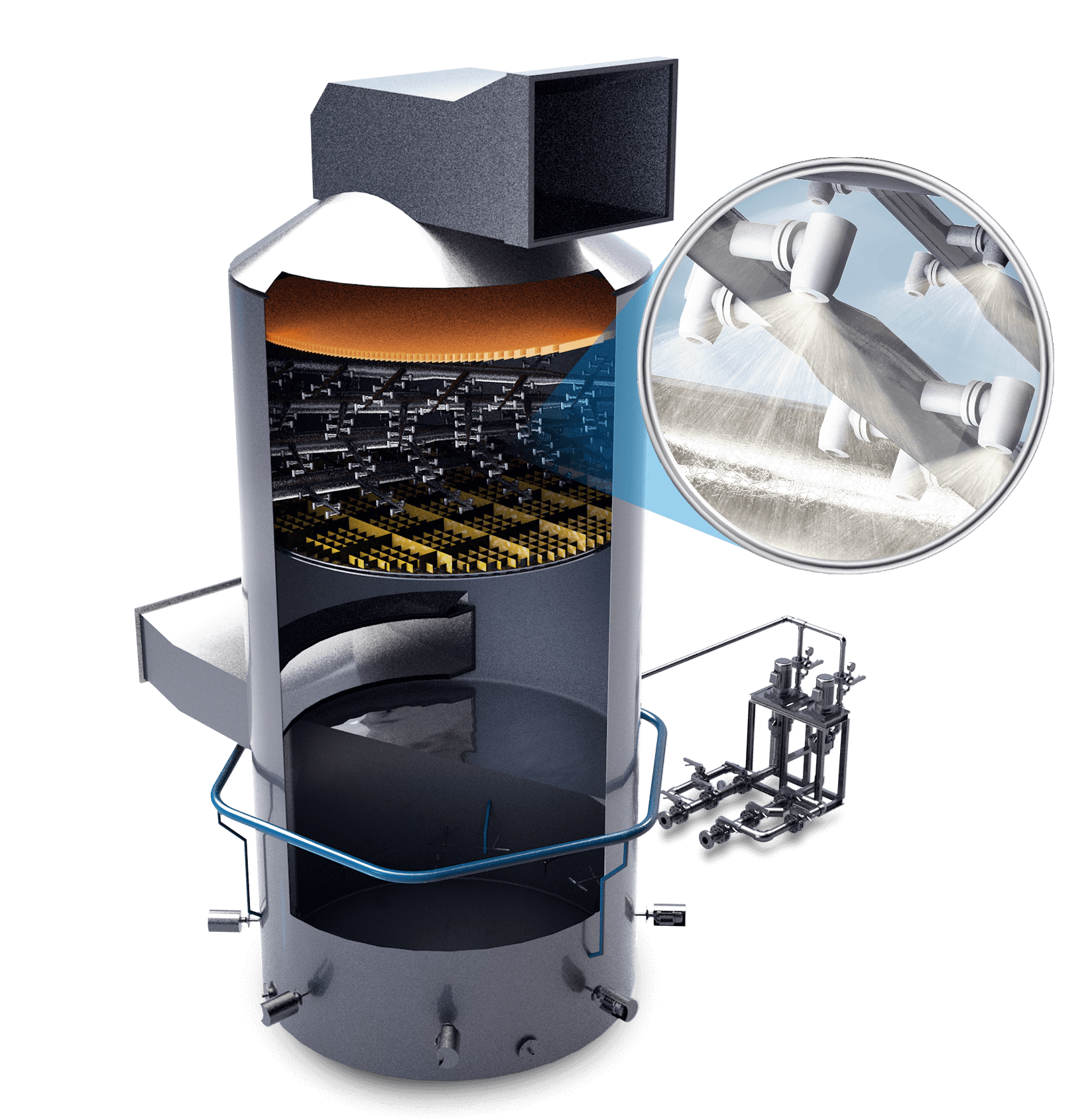
Important factors to consider:
Scrubbing media density and viscosity
Required droplet size
- The correct droplet size is essential to ensuring proper absorption rates
Nozzle material
- As the flue gas is often corrosive and the scrubbing fluid is frequently a slurry with high solids content and abrasive properties, selecting the appropriate corrosion and wear-resistant material is important
Nozzle clog resistance
-
- As the scrubbing fluid is frequently a slurry with high solids content, selection of the nozzle concerning clog resistance is important
Nozzle spray pattern and placement
- To ensure proper absorption, complete coverage of the gas stream with no bypass and sufficient residence time is important
Nozzle connection size and type
Required scrubbing fluid flow rates
Available pressure drop (∆P) across the nozzle
- ∆P =供应压力喷嘴入口——过程之前ssure outside nozzle